How To Solve Casting Defects And Suggestion Tips
How To Solve Casting Defects And Suggestion Tips
1 cold flow
Increasing casting temperature, reduce filling time, add gate size, improve air venting condition. china mold Find the right aluminum alloy, silicon contains over 10% aluminum alloy will have good liquidity.
2 sinks
Different aluminum alloys have different shrinkage rates, find minimum shrinkage rate aluminum alloy for your casting products. Alloy aluminum shrinks less than pure aluminum, we suggest ADC14. The material of ADC14 Si contains 16%-18% Cu contains 4%-5%. And the same time reduces casting temperature and mold temperature.
3 blisters
Many blisters problems caused by ejector parts from the cavity, not the right time. To early ejector, parts will have not enough time solidification, keep products in mold cavity more few seconds.
Reduce mold temperature and check the mold temperature is equably or not, and prevent part mold overheating.
4 laminations
Poor mold rigidity, a problem caused by mold plate shake during casting, the pressure die casting mold base very important for die casting products quality, professional die-cast mold maker will seriously to handle every step in the quality die-cast mold.do not use QT550 or QT600 for your die casting mold base, most china die-cast mold makers will purchase S50c material for their aluminum die casting mold.
5 warping
First, we need to recheck the ejector pin to locate is the right place. Any deflect ejector will make casting parts a bending problem. Check stack-up products is the right way. Particularly for large and thin walls products. Like the die-casting aluminum light shell, the normal light shell was thin walls die casting parts.
6 shrink porosity
Reduce casting temperature, and looking the low melting point aluminum alloy, increasing injection pressure. Many aluminum dies casting manufactory casting big parts by small size cold chamber die casting machines. Before batch production Please Calculated part weight and analyze the project area.
7 cracks
Cracks problem caused by many cause. Check the mold first, check aluminum alloy chemical composition if mold has no any problem, any chemical ratio imbalance will make cracks problem, so control smelting furnace temperature stable is critical. At the same time increasing mold temperature.
8 gas porosity
Increasing air vent size, add filling time, let air have enough time to escape from the mold cavity. Recheck your lubricant spray is right or possible too much spraying.
We are Aluminum die casting mold suppliers. If you are interested in our products, please feel free to contact us.In addition, we can also provide customized Aluminum Die Cast Mold Accessories.
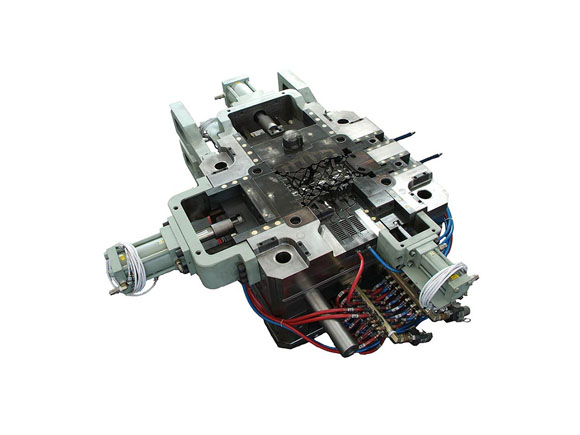